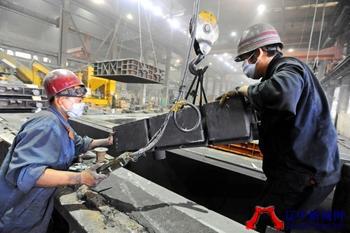
In 2009, the country’s machine tool output value was the largest in the world with more than RMB 400 billion, but the industrialization level of high-end CNC machine tools in China is still not high, and the foundation of a large number of machine tool manufacturers is still very weak. The high-end CNC machine tools needed in the domestic market are still It mainly depends on imports.
Taking metal cutting machine tools as an example, although the total value of China's imported gold-cutting machine tools as a percentage of the total value of domestic gold-cutting machine tools is decreasing year by year, the total value of imported gold-cutting machine tools has remained unchanged. The industries that import these high-end machine tool products mainly focus on key industries such as aviation, aerospace, energy, shipping, and automobiles. Their performance requirements for machine tools are high, especially for machine tool movement accuracy, movement speed, operation stability, and intelligent monitoring. The requirements are much higher than other industries.
Taking the aircraft manufacturing industry as an example, the processing of parts and components in this industry mainly uses five-axis CNC machine tools. Therefore, there are unique requirements in multi-axis linkage accuracy, part processing consistency, and network-based fault diagnosis. In terms of machine tools, the above technical aspects still need to be improved. In general, the domestic machine tool industry has a large gap in user process research, industrial structure, and technology R&D.
On June 16, 2011, the U.S. Department of Commerce announced the implementation of the "Exceptional Regulations for Strategic Trade Licensing," which excludes China from 44 countries and regions that enjoy trade facilitation measures. With the enhancement of domestic enterprises’ innovative capabilities, governments and enterprises in developed countries such as the United States, Japan, and Germany have increased their awareness of Chinese companies’ prevention and increased their control over the export of advanced technologies and equipment to China. The industrial chain of the machine tool industry is long, and one link is “clampedâ€. The development of the entire industry is constrained.
"The cost of importing advanced technology and equipment in China has risen sharply." According to Luo Baihui, secretary-general of the International Mould and Metals and Plastics Industry Suppliers Association, the average unit price of imported metal sheet machine beds has increased from 67,000 USD in 2007 to 2010. 111,000 US dollars. Statistics from the General Administration of Customs show that from January to May 2013, China's cumulative imports of metal processing machine tools 32,079 units, compared with the same period last year decreased by 21.5%, the cumulative amount of imports reached 4.408 billion US dollars, down 16.8% year-on-year. The number of metal processing machine tools imported was 6,604, with an import amount of 744 million U.S. dollars.
In addition, under the background of no obvious signs of recovery in the global advanced economies, China’s machinery industry will face more challenges in the global competition landscape, frictions will be more frequent, and will further spread from low-end products to high-end products. From product trade links to the institutional environment, from a single "two anti-one protection" trade remedy investigations to intellectual property rights, technical barriers to trade, industrial competitiveness investigation and other means to spread. Before the outbreak of the financial crisis, the domestic market share of the US equipment manufacturing industry, which has been declining, has risen from 67.4% in 2007 to 69.72% in 2010.
With the increasing demand for various special machine tools in the global market and the increasing complexity of technical requirements, companies are urged to improve their own product development process. The management hopes that employees in different departments will work in the form of integrated project teams to increase work efficiency. Machine tool companies want to combine various IT systems into a complete software package and provide them to customers. In this regard, Luo Baihui stressed that machine tool manufacturers should not ignore the increasingly strong growth of mid-range technology areas, because the new industrial countries are increasingly producing their own mid-range technology products.
China's high-end machine tool market has always been dominated by the United States, Japan, and German companies. The mid-end market is mainly divided by Taiwan's machine tools, mainland machine tools, and Korean machine tools. German machine tools, regardless of machine tool performance or manufacturing process, can be referred to as the “big brothers†of the industry. If they enter the mid-end market, they will have a considerable impact on non-German companies. Chinese domestic machine tools are mainly concentrated in the low-end market. Although Chinese companies gradually move closer to the mid-end market, the mid-end market is still dominated by Taiwan and South Korea. In the long run, the mid-end market is a direction that Chinese companies must explore in the future. Obtaining a place in the mid-end market and stably expanding market share are crucial to the development of the Chinese machine tool manufacturing industry. At the same time, it is also an inevitable step on the way to the high-end market.
Strengthening cooperation with the Taiwan machine tool industry is one of the ways to resist the large-scale invasion of German and other foreign companies. In recent years, the machine tool industry in Taiwan has developed rapidly, maintaining a growth rate of over 60%, and ranking sixth in the world market. In 2011, the output value of Taiwan's machine tool industry reached 5 billion U.S. dollars. It is the sixth largest production area and the fourth largest export zone for machine tools in the world. In 2012, the export value reached 4.236 billion U.S. dollars, which is expected to surpass Italy and become the third place behind Japan and Germany. Large machine exports. In Taiwan, the value of the machine tools exported to China mainland and Hong Kong each year is approximately US$1 billion. In 2012, the number of machine tools exported to China was US$1.431 billion, accounting for 33.8% of all exports.
Strengthening the cooperation model with Taiwanese companies and emphasizing technical exchanges have a positive effect on improving the manufacturing capabilities of Chinese companies. Mainland Chinese enterprises should pay attention to opportunities, seize opportunities, and put forward more cooperation projects on technology introduction and exchange.
Die Casting Mould,Die Cast Mold,Die Casting Mould Parts
Ningbo Beilun Huari Metal Products Co., Ltd. , http://www.huari-metal.com