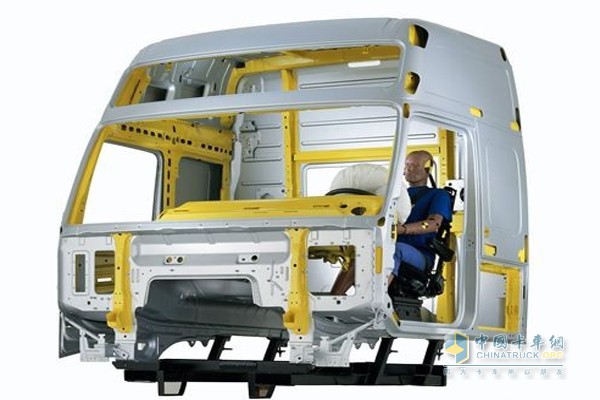
According to Eurostat's freight statistics, since January 2016, nearly 75% of the goods in Europe each year have been transported by road. This fully proves that road freight is more cost-effective and convenient than rail and air freight. Obviously, over the years, road freight is very popular, and commercial vehicle manufacturers are now constantly exploring and practicing various methods to reduce vehicle weight. The factors driving this move are mainly twofold: First, to save fuel costs, and second, to meet the increasingly stringent emission limits that the European Union is establishing.
The link between vehicle weight, fuel consumption, and engine emissions is inextricably linked; the heavier the vehicle, the more fuel it consumes at the same transport distance, the higher the cost, and the more fuel it consumes, the more emissions it generates. the amount.
Therefore, fleet operators and truck manufacturers are constantly searching for better-performing vehicles, reducing fuel costs and reducing emissions.
material selection
With increasingly fierce market competition, aircraft manufacturers must continually improve the design of aircraft and aerospace components. Especially in recent years, the cost of aviation fuel has continuously increased and the industry has been greatly impacted, which has brought this demand to a new height. Airlines continue to exert pressure on aircraft manufacturers to seek more efficient ways to reduce fuel costs. This means that all airplanes used traditional steels such as steel and aluminum to make airplanes. Now, engineers have introduced a variety of lightweight materials and composites to replace certain aircraft parts. This new solution offers the same or even better performance in terms of robustness and durability.
Commercial vehicles must be strong enough to carry the load of cargo, meet the daily harsh conditions of transportation, and ensure an appropriate level of safety. People often think that heavy vehicles should be made of heavy materials. However, there are more and more lightweight alternative materials available nowadays, and there are more and more applications, some of which have been used in other industries such as aerospace and racing. With the reduction of raw materials and process/manufacturing costs and increased availability, these solutions can greatly increase the weight ratio of load bearing parts.
Truck manufacturers have begun to use aluminum and other lightweight metals instead of heavy metal materials, but plastics, carbon fiber reinforced polymers and other non-metallic materials are the latest development focus.
Carbon fiber is very sturdy and extremely lightweight. Its strength is five times that of steel, its hardness is twice that of steel, and its weight is only two-thirds that of steel. The extremely fine carbon fibers are wound together like a yarn to form a permanently shaped layer of fiber that can be overlaid on the mold and form a coating with the resin or polymer.
However, the production cost of carbon fiber components is still daunting, and automakers usually adopt another more practical compromise strategy - plastics. In recent years, plastic molding technology has significantly improved in temperature performance, strength and hardness, providing truck manufacturers with more possibilities for weight reduction. In addition, the flexibility of plastic design - achievable shape and form - is much greater than metal parts. It is also possible to use plastic encapsulating materials to combine plastic and technical components. This is especially useful in situations where fasteners, such as threaded inserts, are required to attach other parts to plastic molding, as opposed to "snapping" fixation methods.
Optimize vehicle system solutions
Today, we can see that more and more plastics and other non-metallic parts are being integrated into the design of trucks. The complete redesign of vehicles using different materials represents a kind of thinking transformation and is a long-term goal. In the short term, the focus will be on using the system design to reduce weight as much as possible. Truck designers need system suppliers to redesign new systems and subsystems in a more forward-looking manner, with weight loss as the main design element.
Energy-saving and emission-reduction requirements are increasingly important, and more and more systems may be redesigned to produce more simple and efficient vehicles. By developing innovative components, it helps eliminate other unnecessary features or components.
Parker Hannifin, a specialist supplier of custom motion control solutions for the global truck market, plays an important role in providing innovative systems for automotive manufacturers that can reduce weight, integrate subsystems with a variety of different functions, and do no harm. Simplify assembly with performance and reliability.
Looking to the future of technology and technology
In addition to lightweight materials and optimized solutions, other emerging elements will also help shape future car designs.
3D printing
3D printing is a manufacturing trend that will definitely affect the design and development of future automotive parts. With the continuous reduction of related costs, this technology will also be more and more applications. The process itself is designed to build a layer of deposited material to get the finished product.
A large number of F1 racing cars have used 3D printing technology to make lightweight rolling rings, non-carbon brake air inlet floor parts, and more. The rolling ring is used at the highest point of the car, minimizing the impact on the car's low center of gravity. They are very important to the integrity and safety of the car's structure, so they need to be both robust and lightweight.
Electric cars and hybrid cars
The ultimate solution to the fuel saving problem may be to completely remove the fuel from the equation and design and manufacture all-electric vehicles. We are seeing more and more new-design medium-sized goods vehicles and the development of electric vehicles in urban small-scale vehicles. Nowadays, more and more heavy-duty electric vehicle designs have emerged.
The replacement of the internal combustion engine by a system of motors, servo drives and accumulators, which is lighter and has significantly reduced the weight of the vehicle, does not take into account that the all-electric system completely eliminates the weight reduction required for storing the liquid fuel in the vehicle.
The challenge lies in the development of battery technology that allows vehicles to run longer distances after charging, or systems that charge themselves through regenerative braking and other processes. The new research has led to the development of a series of new battery technologies, including rechargeable Lithium Lithium, which features light weight and high gravity energy density. Using this technology, companies involved in R&D are actively developing the electric vehicle target market, which greatly expands their application range.
While waiting for the commercial launch of all-electric trucks, truck manufacturers can also use some of the existing electronic technology developments, including the use of hybrid electric solutions.
All-electric plug-in vehicles may be more suitable for local transport fleets or specific applications, such as garbage collection vehicles, at least in the near future. For long-distance transporters, hybrid vehicles will increasingly be selected in the coming years. .
Of course, there are other solutions to reduce the use of internal combustion engines, such as electric pump steering solutions, which can reduce the need for supporting equipment to power the engine, and support the reduction of engine displacement, thereby reducing the weight.
to sum up
Perhaps the greatest opportunity to reduce global carbon emissions is in the hands of today's truck manufacturers and the suppliers who produce components and subsystems. As one of the largest emitters of greenhouse gases, the road transport industry has the responsibility to support increasingly stringent legislation. When designing each new type of vehicle, it should first consider reducing the weight, whether it is the external body or the systems and components therein.
For manufacturers, one of the keys to success is working with innovative suppliers that support the development and implementation of new technologies. Visionary thinking, coupled with the drive to explore, develop and apply simpler, newer technologies, in the near future, our roads are powered by light-weight cars with clean technology that send a wide variety of goods to use. Or sales location.
Germany Man Group was established in 1758. The three letters MAN consisted of the first letter of the company's former "Maschinenfabrik Augsburg Nurnberg", Headquartered in Munich, Germany, is a leading European engineering group with approximately 52,500 employees working in the five core areas of commercial vehicles, industrial services, printing systems, diesel engines and turbines in 120 countries in the world, providing comprehensive solutions, Annual sales of 16.5 billion euros (2011). Man Group has established joint ventures and other partnerships with local companies in India, Poland, Turkey and the United States. Is one of the world's top 500 group.
Man Engine Sealing Products
Man TGA Head Gasket, Man TGX Engine Gasket, Man 2866 Head Gasket, D2540 metal Head Gasket
HAFID INTERNATIONAL LIMITED , https://www.hapgasket.com