Baosteel Stainless Steel 1780 hot-rolled descaling system was designed by Mitsubishi Corporation of Japan. High-pressure descaling motor was manufactured by Japan Mitsubishi and Shanghai Electric Machinery Factory. China Metallurgy Saidi was responsible for engineering design. The system was officially put into operation in December 2003. The rolling steel grades of Baosteel Stainless Steel 1780 Hot Rolling Mill are stainless steel and carbon steel. The working time of descaling pump is about 6,935 hours, and the descaling of carbon steel is about 4435 hours per year. The descaling of stainless steel is about every year. It is 2500 hours.
Descale is a very important process in the hot rolling process. The descaling system is composed of descaling pump and injection valve. Its role is to remove the oxidation of the hot billet during the heating process through the powerful impact force of high pressure water. Tin skin and secondary iron oxide skin regenerated during rolling, thus ensuring the surface quality of the finished steel product. The descaling pump flows the water to the mother tube, and the descaling process is completed by the opening of the injection valve on the mother tube.
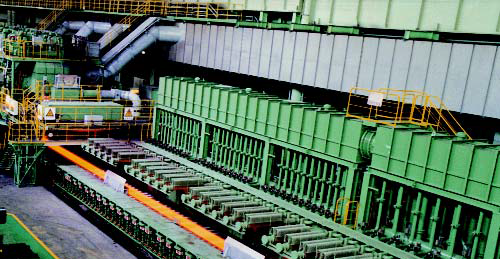
Second, descaling process introduced
There are four groups of injection valves on the hot rolling line. The descaling points are descaling box inlet, outlet descaling (HBSa+HBSb), rough mill inlet descaling (RMa), export descaling (RMb), finishing mill inlet, Export descaling (FSBa+FSBb). The descaling point water demand is: the descaling tank inlet and outlet descaling nozzles need 3630L/min, the roughing mill inlet needs 3250L/min, the roughing mill outlet nozzle needs 3250L/min, the finishing mill upper and lower nozzle needs 4200L/min.
Different products of carbon steel and stainless steel and different production rolling rhythms change the quantity, location, and flow of descaling at any time. The judgment of descale point is judged by the line position of the billet on the production line. The more descale points, the more the injection valve is opened, the higher the pressure requirement of the parent pipe.
The scale removal system is also provided with a 10m3 balance gas water tank and four descaling pumps adopt the common parent pipe method.
The outlet pressure of the manifold changes between 18MPa~22MPa. The descaling pump works in two states: one is the descaling state, requires a pressure of 18 MPa, and the other is a non-descaled state. When the descaling pump flow is lower than 110 t/h, the thermal protection bypass valve is opened and the water is turned off. Flow into the trench, which is to prevent the injection valve closing when non-descaled, resulting in boring pump situation.
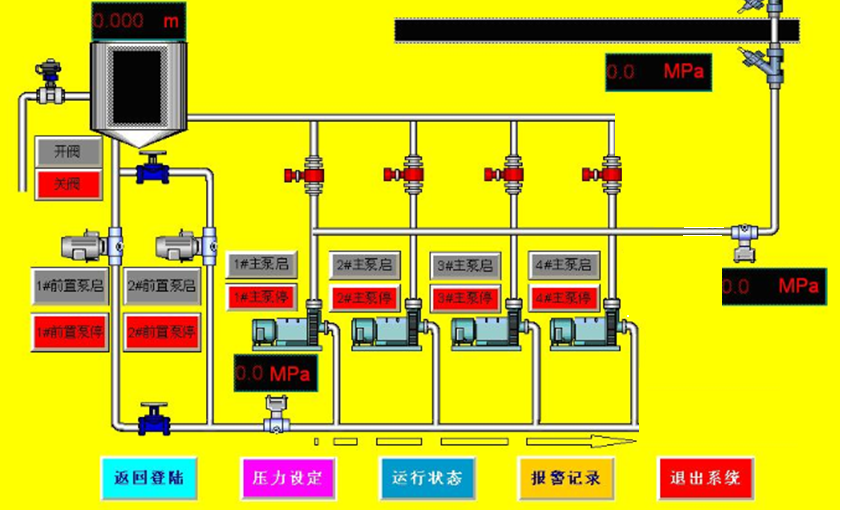
Third, equipment parameters
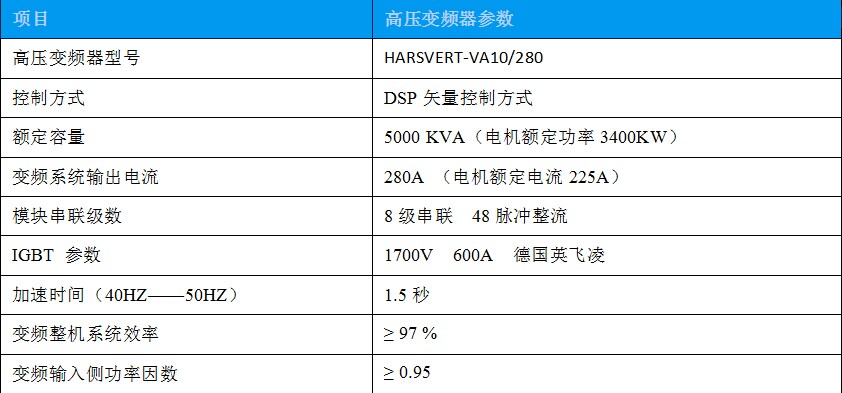
Fourth, there are problems and solutions
Baosteel's stainless steel hot rolling mill is equipped with four descaling pumps, which are used in normal production with three to one standby. Before the transformation, the four descaling pumps are all started with the frequency of the reactor. However, the descaling pump motor starts at each power frequency. In the descaling process with water spray, the rapid change of load produces a strong inrush current, which generates a great impact on the rotor of the motor and damages the internal of the motor, which reduces the service life of the motor and affects the normal operation of the rolling line. In addition, since the descaling high-pressure water pump operates at constant power frequency, the water flows into the trench through the bypass valve in the non-descaled stage, which can not meet the different demands of different steel descaling on the system pressure and the flow under no-load conditions, resulting in a large number of Electricity and water resources are wasted.
After many demonstrations, in the end, in 2009, Baosteel selected Beijing Leader Huafu high-voltage frequency converter products to carry out frequency conversion modification of the 1# descaling pump to regulate the flow, and the remaining three pumps were still the original frequency setting mode with reactors.
V. High-voltage inverter parameters
Taking into account the large impact force of the descaling pump motor and the frequent fluctuation of the load torque, according to the requirements of the moment of inertia of the motor and the load, the nT curve of the motor and the load, and the time of acceleration and deceleration, the high-voltage inverters of the Leadwell company have The following enlarged selection:
Project high voltage inverter parameters
High-voltage inverter model HARSVERT-VA10/280
Control mode DSP vector control method
Rated capacity 5000KVA (motor rated power 3400KW)
Frequency conversion system output current 280A (motor rated current 225A)
Module series series 8 series 48 pulse rectifier
IGBT parameters 1700V600A Infineon Germany
Acceleration time (40HZ - 50HZ) 1.5 seconds
Frequency conversion machine system efficiency ≥97%
Frequency conversion input side power factor ≥ 0.95
Sixth, the frequency changer control plan
At present, the inverter has two automatic control modes. One is based on the descaling point control. When there is one descaling point, the inverter is controlled to run at 45HZ. When there are two or three descaling points, the inverter runs. At 48 Hz, when there are 4 descaling points, the frequency converter runs at 50 Hz. The other is to perform closed-loop control based on pressure and maintain the parent pressure at a constant value, which is set by the operator depending on the type of steel being produced. When in the non-descaled state, the descaling pump operates at a minimum frequency.
There are two cases of descaling:
1. Each steel billet descaling is finished, waiting for the next billet, the interval is about 20s;
2. The roller on the production line is worn out and needs to be replaced frequently. It needs to change the roller 8 times every day for 15 minutes each time. This process does not need descaling, and the running frequency can be run to the minimum frequency.
When descaling is started after the above two conditions are completed, the frequency needs to be raised from the lowest frequency to the given frequency immediately. The minimum frequency currently set by Baosteel Stainless Steel is 30HZ.
Seven, energy-saving effect
From the formula:
The annual energy consumption of a single descaling pump in frequency conversion:
Energy consumption at high speed: 2800KW
Energy consumption at low speed: = 804KW (considering motor and inverter efficiency)
The overall energy consumption = 2800×70%+804×30%=2201KW
3, energy-saving rate
Saving rate = (2800-2201)÷2800≈21.4%
Eight, frequency conversion transformation experience
The current working method of Baosteel's descaling system is the operation of two industrial frequency pumps and one variable frequency pump. Due to the use of a common mother tube, the two industrial frequency pumps are always running at 50 Hz, while the frequency conversion pump constantly adjusts the frequency and observes from the flow. The frequency conversion pump can only compete with the power frequency pump flow when it is running at 50HZ, but the frequency conversion pump flow will be much smaller when it is running below 50HZ. This is equivalent to a very small output of the variable frequency pump, which is the common operation of the frequency conversion pump and the industrial frequency pump. The inevitable result.
If all four pumps are changed to variable frequency control and adjusted together, the effect will be much better, and the low speed can be reduced to a lower frequency. Baosteel Stainless Steel is constantly exploring its experience, and will also have the intention to transform the frequency conversion of 2# and 3# descaling pumps in the future.
Nine, Baosteel's other achievements of phosphorus removal pump
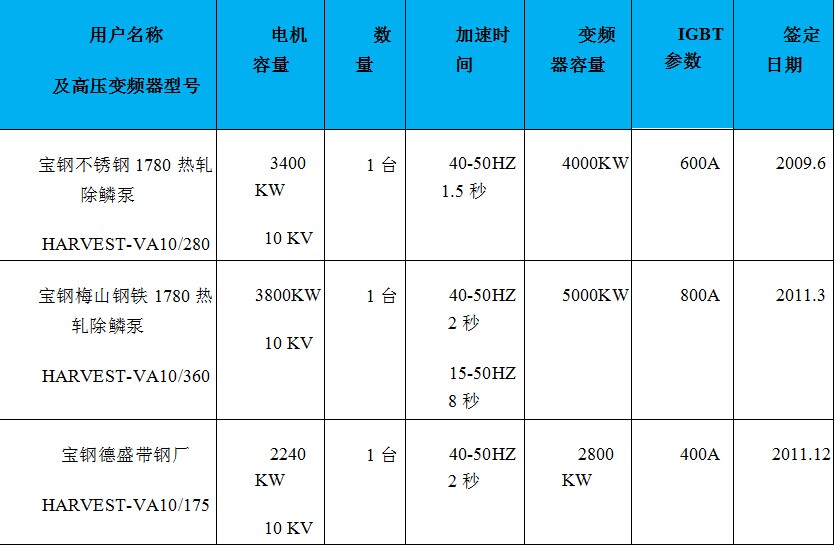
We can supply big range of such bronze Casting Parts, including investment casting and Sand Casting
Sand Casting method (Sand Casting)
Using Sand as Mold material, according to the different components of Sand can be subdivided into wet Sand casting method of Green Sand Mold), surface Dry Sand casting method (Dry Sand Mold), and so on, but not all are available in the casting.
Advantage is lower cost, because the sand mold use reusable;
Lost wax Casting, Investment Casting
This method can be as the outer membrane casting method and the solid casting method.
To copy wax casting items required first, and then into the pool with ceramic and stay dry, make with wax replica is covered a layer of ceramic outer membrane, repeat steps until enough to support outer membrane casting process (about 1/4 inch to 1/8 inch), then the wax melting mould, and out of mold. Then mold need to high temperature for many times, enhance behind the hardness could be used in the casting.
This method has good accuracy, can be used as a high melting point metal, such as titanium casting.
B. Main particulars
|
MAIN PARTICULARS |
Material for product |
bronze |
Standard |
ASTM, ASME, DIN, JIS, ISO, BS, API, EN |
Certificate |
ISO9001 |
Dimension |
As per drawing, as large as we can |
Processing |
Step1:investment casting or sand casting Step2:turning, milling, drilling, grinding, threading, CNC Machining, boring |
Finishing surface |
Machined surface with oil, blasting and painting, anodize, polishing, powder painting, electrophoretic coating- |
Marking |
as per clients` requirements |
Inspection |
material, construction, dimension, heat treatment, hardness, NDT |
Quality |
ISO9001, PPAP control production |
Lead time |
20-30 days for sample, consult with customer for mass production |
Delivery |
Express for sample, ocean shipping/air for mass production |
Our Capabilities |
CNC machining, CNC center machining, drilling, milling, turning, grinding, tapping, boring |
Engineering & manufacturing services |
R&D process, tooling and gauging design, product design Integrated CAD/CAM system, test and measuring |
Others |
Recyclable, in line with environmental requirements and standards, and reliable |
C. Construction
Construction by casting and machining
D Workmanship
The workmanship have good production practice. Care are taken to ensure High accuracy and smooth surfaces
E. Certificates
- Material certificates
- Measuring reports
- Inspection protocol
- NDT reports
- Fixed certificate: ISO9001 certificate
Our service
Besides above the general specifications, we can also supply some specific machining parts as clients' requirements.
Package and shipping
Export cartons, pallets, wooden cases, Polybags
container package and container transportation
Bronze Casting Parts,Oem Bronze Casting Parts,Bronze Sand Casting,Bronze Sand Casting Parts
Shinvast Industry Ltd , http://www.shinvastindustry.com